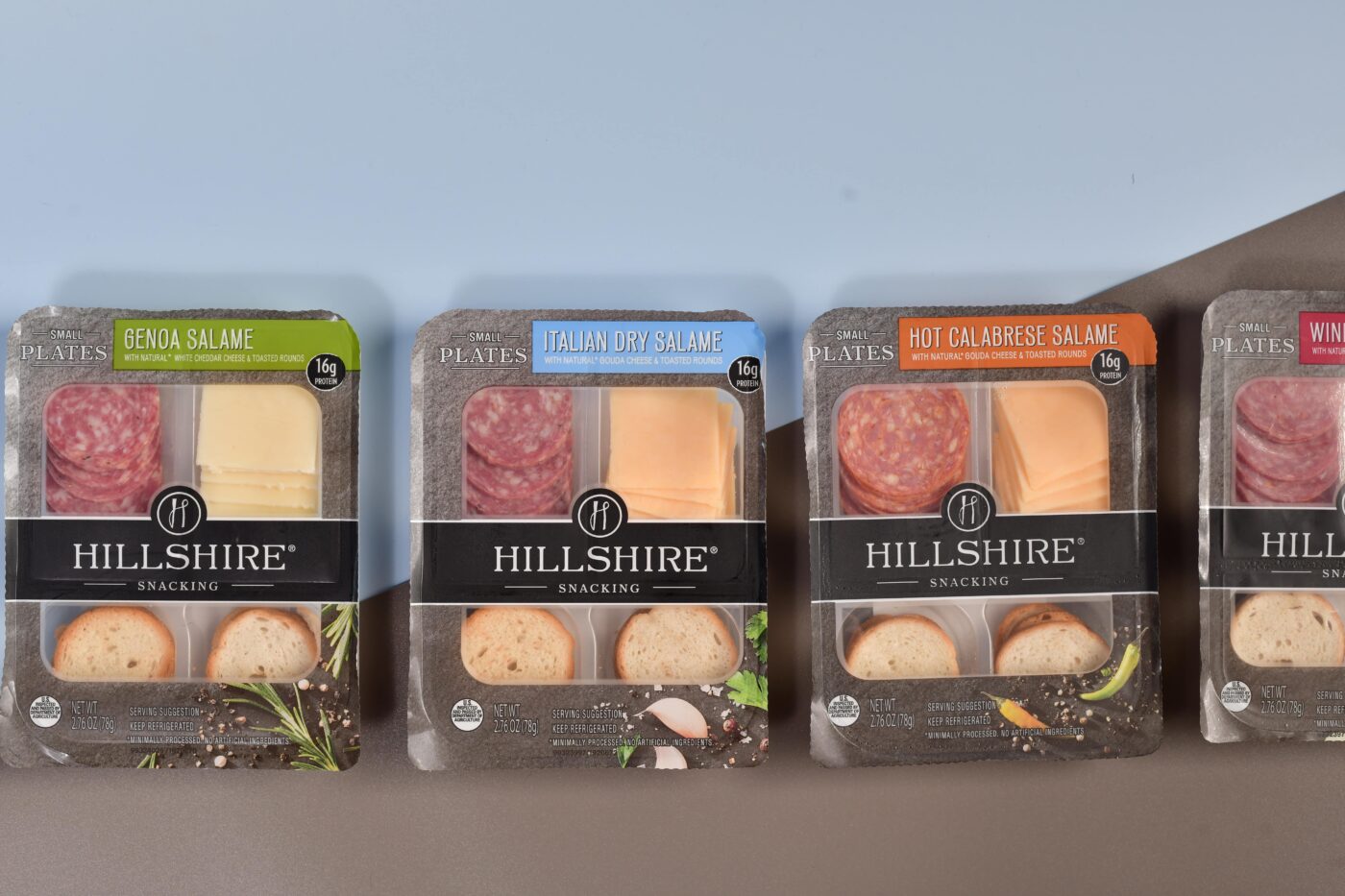
After years of lagging behind more commonly recycled materials like PET bottles,…
Polyethylene terephthalate (PET) and polyethylene terephthalate glycol (PETG) are two similar acronyms representing two very distinct materials. Both of these substances comprise plastics commonly used in the pharmaceutical packaging industry, but their differences in chemical compositions — that is, the addition of glycol — gives PETG more favorable characteristics for highly sensitive packaging applications.
During the heating stage of manufacturing, the presence of glycol helps to prevent the visible hazing, warping, and crystallization effects that typically arise with standard PET. This added resistance to brittleness means that PETG has a slightly softer surface, making it more pliable and highly impact resistant, although it does present a higher risk for damage from scratches and UV light.
Despite these small setbacks, PETG’s properties make it superior for high-intensity production phases, as well as a wide range of applications. It is resistant to heat sealing, thermoforming, and ETO and gamma sterilization — processes under which standard PET would normally crystallize. Not only that but once it’s time to actually package the products, the transparent PETG beautifully showcases each item, while its impact resistance keeps them safe.
PETG’s ability to survive rigorous ETO sterilization processes makes it suitable for sterile barrier pharmaceutical and medical device packaging, as well as FDA-friendly food packaging. Its uses are not confined to high purity applications, however; PETG’s sleek aesthetics and resilience are popular features for RF sealed and heat sealed blister packaging used for cell phones, small electronic devices, and other retail items.
Since 1972, Plastic Ingenuity has been at the forefront of the custom thermoforming industry. Our team has worked extensively with PETG specifically, manufacturing plastic medical trays, as well as our cutting edge 47” catheter delivery system, which enhances product accessibility and eliminates outside impurities.
Our medical device packaging engineering capabilities include GMP procedures, clean room facilities — where we designed our long catheter delivery system tray — and medical grade materials. To learn more about Plastic Ingenuity’s medical device packaging solutions, please visit our healthcare industries info page.