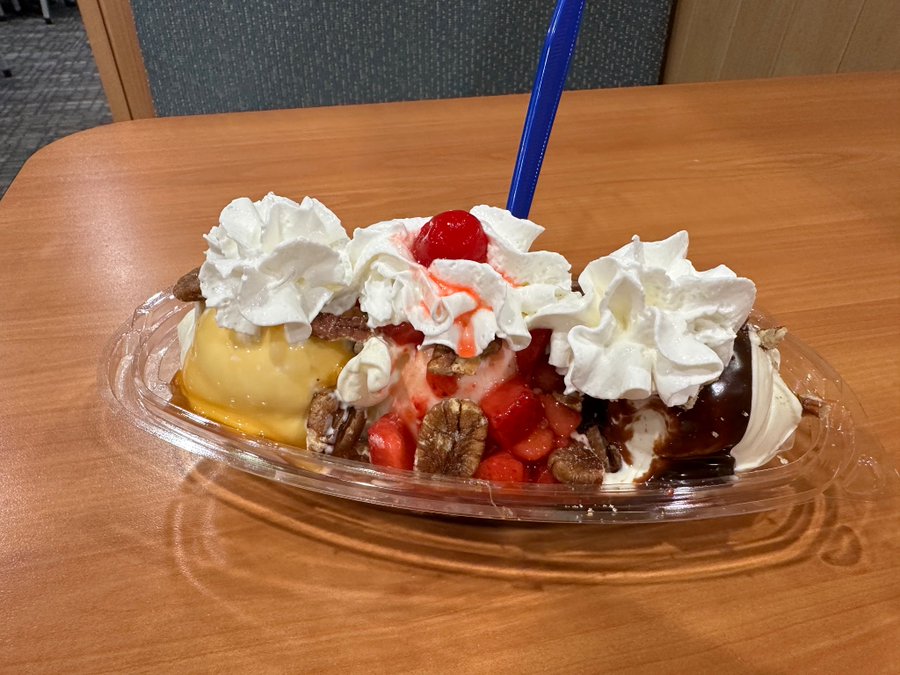
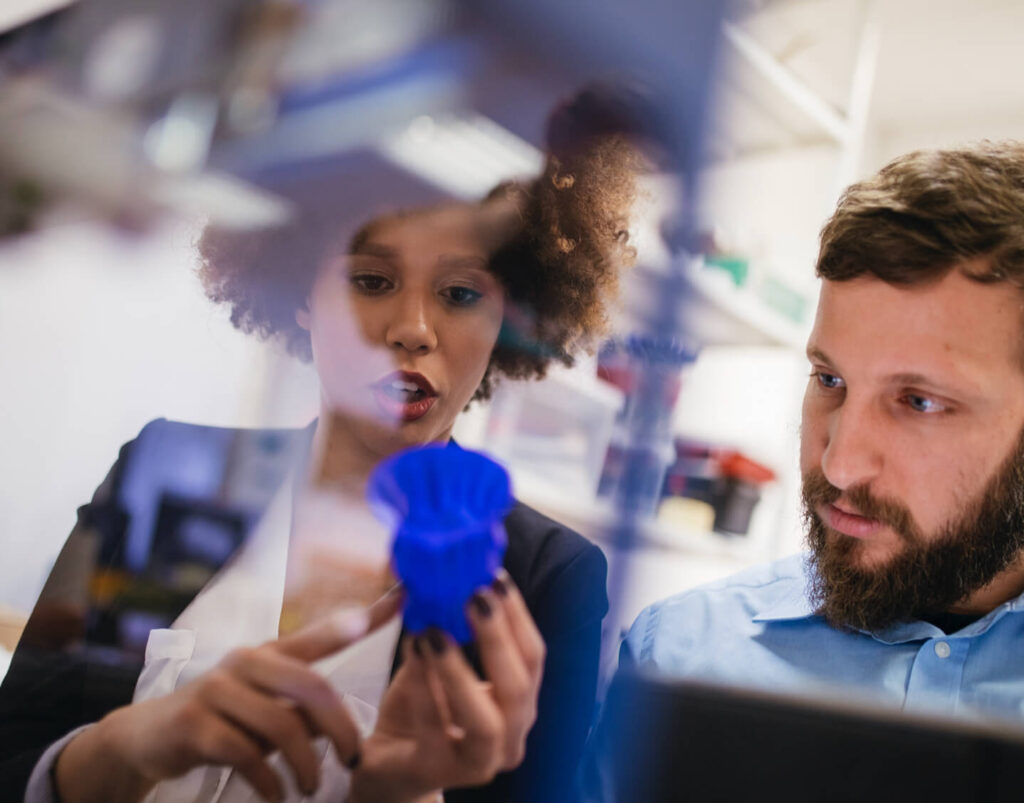
The Challenge
Identifying Unseen Opportunities
Plastic Ingenuity approached a large supply chain and logistics company to investigate the replacement of an origami-style corrugated cardboard insert. Before our investigation, the company used a cardboard box with two folded corrugated cardboard inserts for the packaging of a retail electronic component and its operator manual, accessories, and advertising literature. This component required a manual packing process, in which 27 production line employees had to separate, fold, assemble, load, and label the cardboard box packaging and inserts by hand. In this case, a “less expensive” component created a greater burden to production processes than components considered “more expensive.”
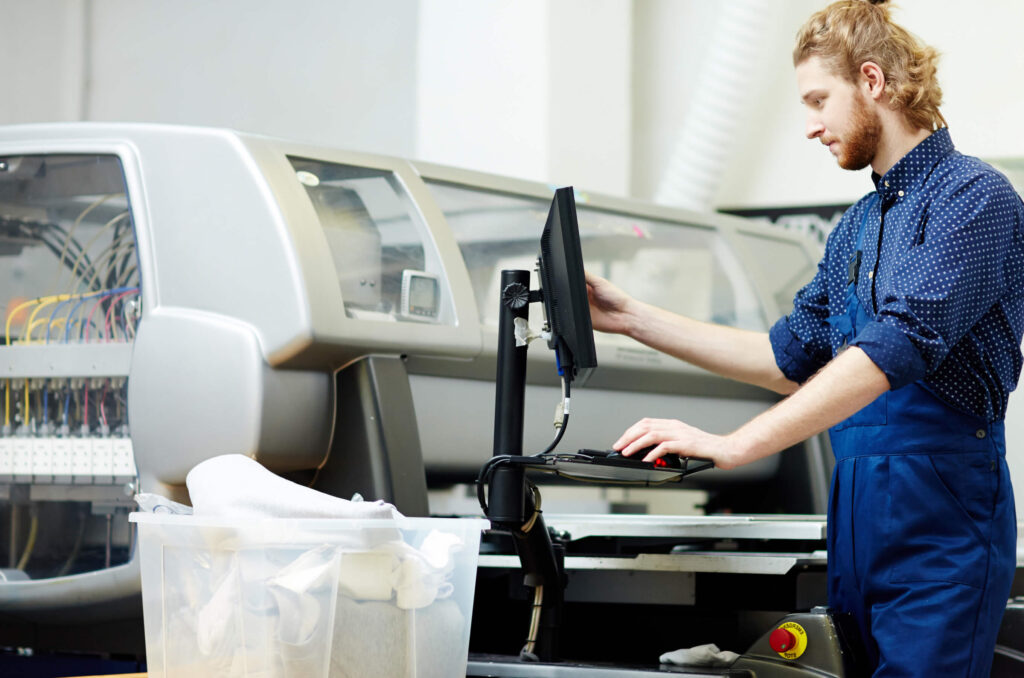
The Process
Folding Efficiency Into the Process
Plastic Ingenuity deployed a team of engineers to investigate the company’s current packaging process, design a plastic component to improve the process, and assist the client in implementing it into the packaging line.
The new packaging plastic part created by our design team replaced the company’s current folded cardboard insert and required no additional folding or assembly by employees. The new insert easily fits within the folded cardboard packaging without compromising the outer shell.
The Solution
A More Elegant Operation
Plastic Ingenuity’s packaging plastic part was much easier to use than the folded cardboard insert. Because of this, the client was able to reallocate employees previously responsible for folding and placing the folded cardboard insert to other line responsibilities, reducing the total number of line employees from 27 to 22. This simple part redesign resulted in significant cost reductions and operations improvements for our client. Our team has generated similar results in other manufacturing and kitting applications, and we’ve partnered with firms across many different industries to improve their performance and results in both automated and manual production environments.
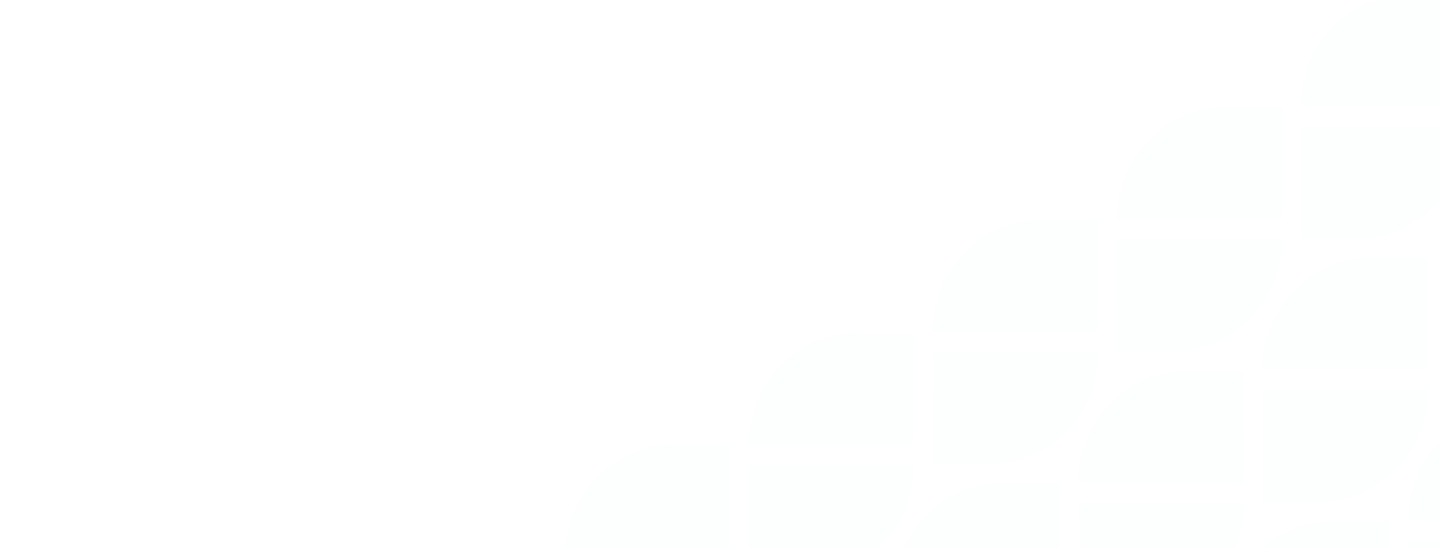
The Results
A Lower Bottom Line
reduction in labor costs per unit.
total savings per month.
lbs reduction in weight per kit.
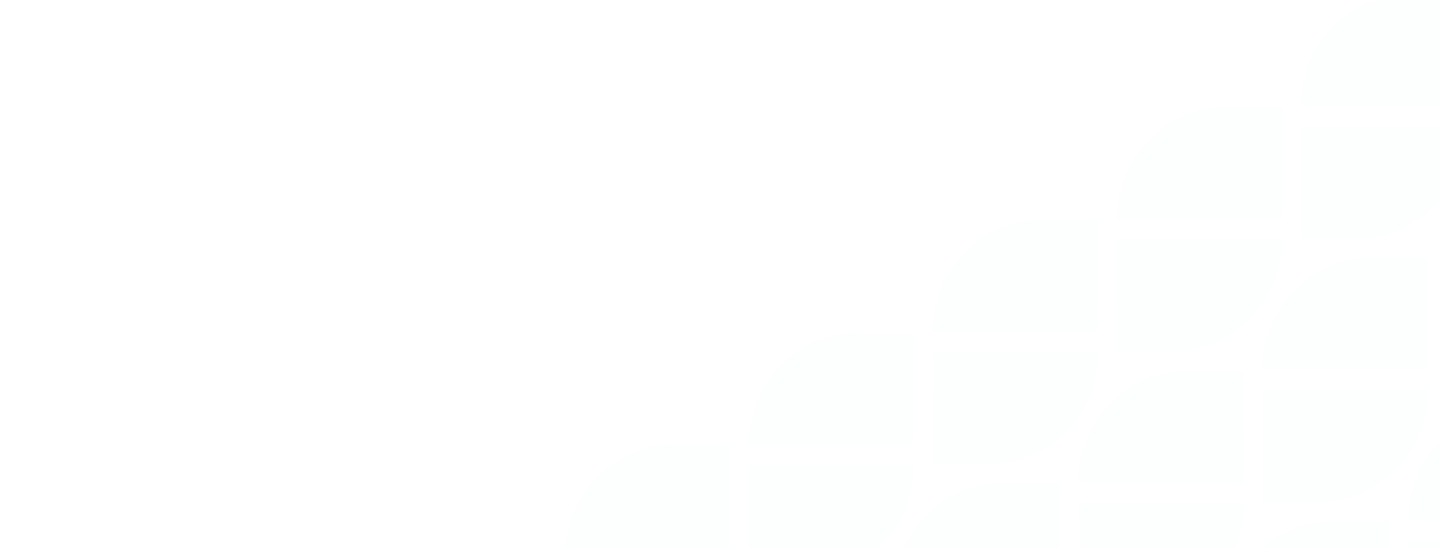