The packaging for your products needs to be both secure and attractive, yet you may not know which packaging design and materials will help you achieve this. At Plastic Ingenuity, we understand the struggle of creating the perfect packaging. We’ve created hundreds of custom thermoformed packaging designs for clients in a variety of industries, so we know the process of determining which packaging can work best for your products. Consult our list of considerations to aid in developing the exact packaging design you need:
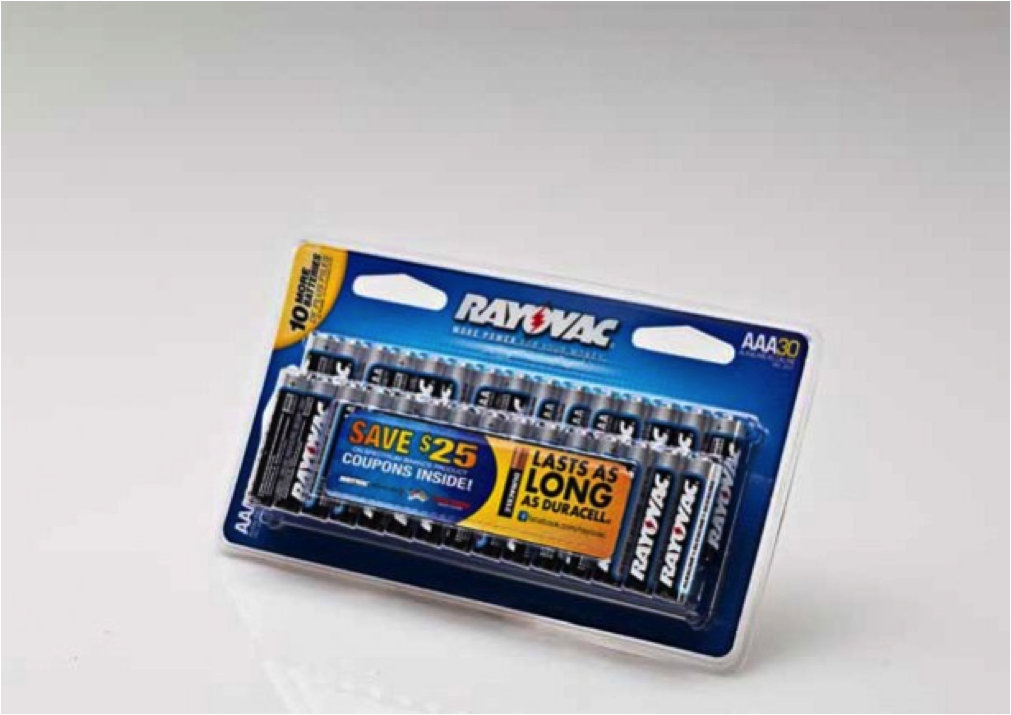
What Type of Packaging Do You Need?
Plastic packaging is not one-size-fits-all; every company should determine its packaging needs to see which model will work best. Plastic packaging is typically broken down into the following styles:
- Clamshell—This plastic packaging design utilizes hinge and press-down features and can be created in stock or custom sizes.
- Tray—Tray designs can be used for packaging that requires a customized shape. During the design process, trays can be developed based on size, shape and strength requirements to fit you products’ needs.
- Blister—Designed for exceptional tamper-resistance, thermoformed blister packaging provides protective strength. This packaging design is often inexpensive to create. Blister designs, which are also available in both small and large sizes, can also house multiple products in one package.
- Tri-fold—Similar to clamshell packaging, tri-fold designs can be snapped together. Retailers can hang this plastic packaging design on a peg or have it stand upright. Either presentation method provides maximum display for products.
- Two-piece—This thermoformed packaging design is commonly used in stock food packaging. Two-piece packaging provides the needed tamper-resistance while still being easy for the consumer to open.
What Type Of Materials Should You Use?
Plastic packaging manufacturers can create your design from a variety of plastic substrates. Some of the most frequently used plastics in packaging are:
- HIPS—Used in both foamed and rigid plastic design, HIPS plastic can be used for custom shapes.
- PET—PET, or polyethylene terephthalate, is one of the most used plastics in thermoforming. Packaging created from this type of plastic has enhanced protections from outside elements.
- PETG—A variation of PET plastic, PETG plastic is a common plastic used in thermoformed tray and blister packaging designs.
- PP—Polypropylene is a rigid plastic that can be used in thermoformed designs.
- PVC—Polyvinyl chloride, or PVC, is the third most commonly used type of polymer. Packaging created with PVC is strong in structure and resistant to harsh impacts and high heats.
- Bio-resin—An eco-friendly plastic option, this plastic option is naturally biodegradable.
Should Your Design Be Custom?
As you decide on your packaging design, consider whether you need it to be customized:
- Yes—Your products have unique shapes, or you simply want a packaging design to match—one that stands out from the crowd. Custom thermoformed designs can resolve this packaging need by adhering to your products’ specific dimensions. Custom thermoformed packaging can also allow you to fit multiple parts into your packaging design.
- No—You need plastic packaging, but it doesn’t necessarily have to be an exclusive design. This is most common for the food and restaurant industries, who simply need deli containers for customers or whose products do not have custom dimensions.
What Size Should Your Packaging Be?
Consider the dimensions of your products when deciding on what type of packaging you need. Custom packaging can be designed specifically to your products’ dimensions, whereas stock packaging is available in predetermined sizes.
What Market is This Packaging For?
Depending on your market and industry standards, plastic packaging may need to meet multiple specifications. See which category your packaging falls into to decide what your packaging design needs:
- Food—Whether it is a stock or custom design, packaging for food products must meet stringent sanitation requirements.
- Pharmaceutical—Many pharmaceutical companies biggest concern is making sure their products’ packaging is adequately protected to avoid outside contamination. Pharmaceutical packaging can be custom-made in clamshell, blister, tray and other designs.
- Medical—Medical packaging is required for storing instruments and other devices. Therefore, it must be highly sterile and protective. Medical packaging oftentimes must also meet specific ISO requirements and be produced in a clean room environment.
- Consumer electronics—Electronics packaging must meet various requirements, including reduced static charge and a retail-ready design.
- Cell phone—Each cell phone has a unique design, and it will need a one-of-a-kind packaging design to match. Thermoformed packaging in either blister or clamshell designs can safely protect mobile phone devices. Clamshell packaging designs are easier for consumers to open, while blister packaging reduces the likelihood of product theft.
- Retail—Retail packaging needs to be protective while still easy to open for consumers. Many companies utilize thermoformed blister packaging for the products they sell. This design provides the custom sizing they need, as well as maximum transparent visibility and product preservation.
- Cosmetics—Cosmetic packaging needs to be attractive enough to draw consumers in while still providing strength for tamper resistance. Blister packaging is commonly used to provide the visibility cosmetics need for sales, yet it still protects products. Companies can also add alluring graphics cards to blister packaging for displaying product information.
Does Your Packaging Need Any Additional Features?
Consider if you need any of the following for your plastic packaging:
- Dust control
- Static reduction
- Heat sealing
- Clean trims
- Ultra precise measurements
- Production that adheres to ISO 9001: 2000 certifications
- Production that adheres to many PPAP requirements
- Prototype production
A custom plastic thermoformer can assure your products are created to any of these specifications.
Final Step: Consult with a Packaging Specialist
After you have evaluated your packaging needs on your own, you will now want to consult with a team of packaging specialists. They’ll have the industry knowledge to go over your responses to our packaging questions and help you create the packaging you need.
Have any additional questions as to which type of packaging you should use for your products? Contact the packaging specialists at PI for further assistance.