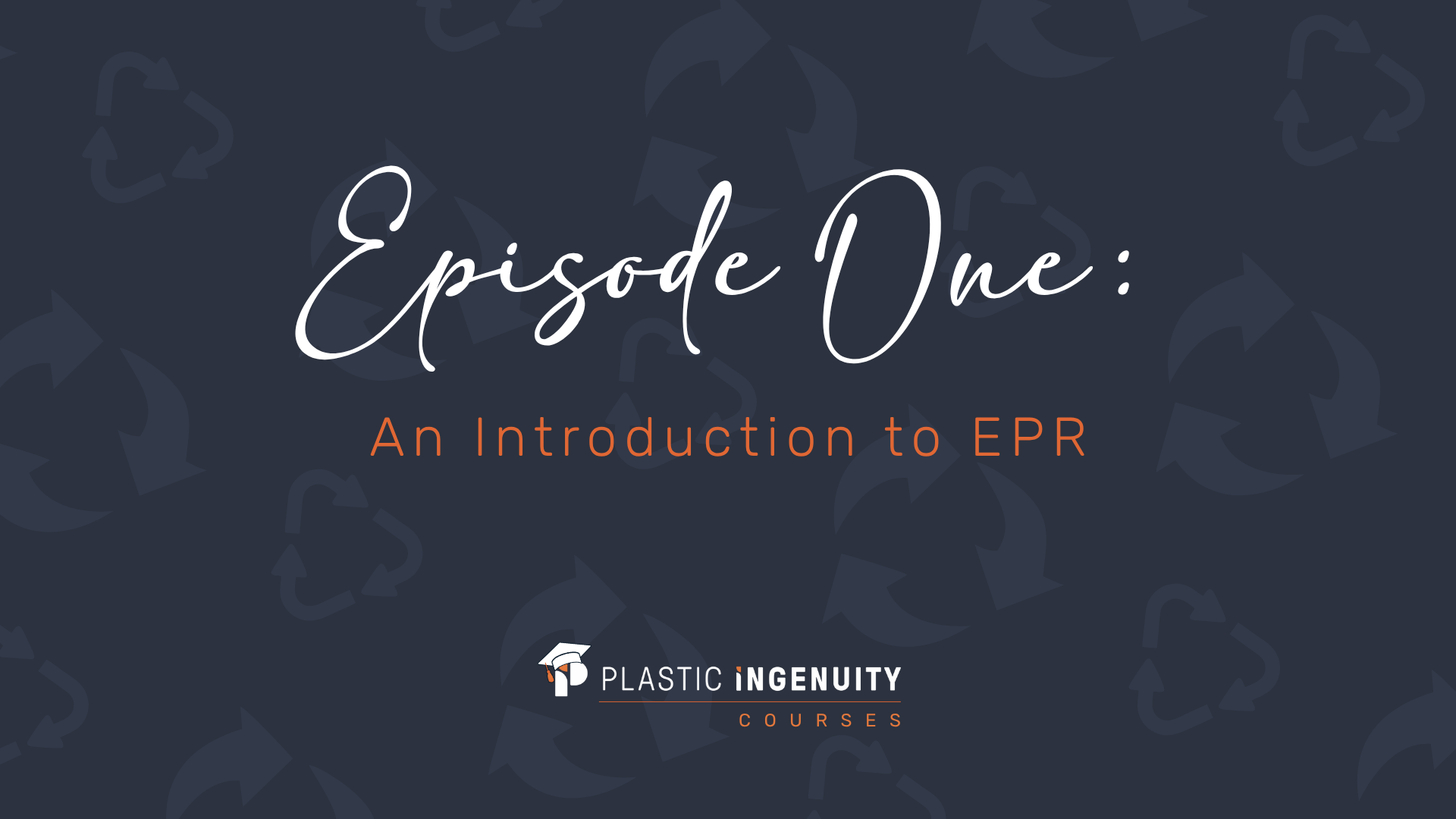
Understanding Packaging EPR: What Brands Need to Know Get up to speed…
Patients who need medical treatment often fear being exposed to harmful germs and unsanitary instruments. Just the thought of a healthcare provider using an unsterilized surgical device or needle is enough to make people feel queasy. As a result, patients find it reassuring to watch a clinician remove healthcare devices from sterile packaging before starting a procedure.
Sterile packaging refers to non-reusable plastic shells, wrappings, and other packing materials that have been terminally sterilized by ethylene oxide (EO), gamma, or autoclave sterilization. Manufacturers use this packaging to ensure that medical devices, instruments, and other healthcare products stay germ-free. Sterile packaging has many advantages for healthcare providers, manufacturers, and patients.
Read on to learn more about the importance of sterile packaging for medical devices and the specific sterilization methods used for them.
The rising demand for medical care has led to a boom in packaging for healthcare products. Experts predict that the global consumption of medical device packaging will increase by 7.4% annually between 2021 and 2031.
In response to this rapid growth, manufacturers have developed innovative ways to produce sterile packaging. The healthcare industry relies on this technology to protect medical devices and products from contamination. Sterile packaging also ensures that facilities and medical device manufacturers comply with industry regulations. Let’s take a closer look at the benefits of sterile packaging in healthcare settings.
Protecting patients from disease is the primary purpose of sterile packaging. Packaging like blister packs and pouches help prevent the spread of harmful germs that can make patients ill or exacerbate their symptoms.
According to the World Health Organization, about 7% of patients in acute-care hospitals contract a healthcare-associated infection (HAI) while receiving treatment. HAIs are most likely to affect vulnerable populations like newborns and people receiving intensive care.
Many HAIs are related to medical instruments like catheters and IVs that have been improperly sterilized and become contaminated before use. The Centers for Disease Control and Prevention have identified these common types of medical device-associated HAIs:
Also, improperly sanitized medical devices can spread bacteria and viruses between patients and providers. For example, patients who receive central venous catheters may develop Candida auris, a yeast that can spread through the bloodstream. Similarly, medical devices like IV catheters and ventilators can increase patients’ risk of developing carbapenem-resistant enterobacterales such as E. coli.
HAIs spread by medical devices can have serious consequences, including:
Medical device sterile packaging plays an essential role in preventing HAIs. Research shows the use of disposable medical devices by healthcare facilities reduces the spread of disease. The medical professional removes the device from its sterilized packaging, uses it once, and discards it.
Sterile packaging ensures that medical devices comply with industry standards. Device creators should search for an expert packaging manufacturer that’s intimately familiar with the specific requirements of the healthcare sector.
The U.S. Food and Drug Administration (FDA) oversees the manufacturing of sterilized medical devices and their packaging. The FDA defines sterile packaging as a container-closure system with a microbial barrier. A container-closure system consists of packaging components like containers, stoppers or screwtops, administration ports, closure liners, and inner seals. These components work together to shield the medical device from germs.
Packaging manufacturers must perform sterility tests to demonstrate that their containers will maintain package integrity and protect products for their whole shelf life. These tests can take several forms, such as:
If you’re in the market for a packaging manufacturer for medical devices, search for a company with a track record of receiving FDA approval for its packaging systems.
The International Organization for Standardization (ISO) also regulates the medical devices industry. Manufacturers who follow the ISO’s stringent quality control standards can receive ISO 13485 certification. Companies must demonstrate their excellence in five areas:
Plastic Ingenuity has received ISO 13485 certification and designs all of its thermoformed plastic packages to conform to industry standards.
Developing sterilized medical packaging is a multi-step process. First, the manufacturer works with the medical device creator to select the best packaging for its product. Popular packaging materials include:
Next, the manufacturer uses one of several techniques for sterilization, such as:
A thermoforming manufacturer can help you determine the most appropriate and cost-effective sterilization method for your medical device.
Thermoform sterile packaging ensures that your medical devices will reach patients safely. Plus, a stylish but functional package brands your product and helps it stand out from competitors. Plastic Ingenuity has four decades of sterile packaging knowledge. Our expert team can offer guidance on every step of the medical packaging process, including design, production, and distribution. Contact us today to get started.